公差0.03
压制方式高压铸造
加工设备CNC加工中心
加工精度精加工
变形温度360
是否库存是
烧结温度305
加工材料铝合金,铜,不锈钢,钛合金
年较大加工能力6522350
是否出口否
CNC四轴加工是一种的数控加工技术,它在传统的三轴(X、Y、Z)基础上增加了一个旋转轴(通常是A轴或B轴),从而实现更复杂的加工操作。以下是CNC四轴加工的主要特点:
### 1. **多面加工能力**
- 四轴加工可以通过旋转工件,实现多个面的加工,减少装夹次数,提高加工效率。
- 适用于复杂几何形状的零件,如曲面、螺旋槽、倾斜孔等。
### 2. **高精度与一致性**
- 四轴加工通过数控系统控制旋转轴,确保加工精度和一致性。
- 适用于高精度要求的零件,如、器械等领域。
### 3. **减少装夹次数**
- 传统三轴加工需要多次装夹才能完成多面加工,而四轴加工通过旋转轴可以一次性完成多面加工,减少装夹误差和时间。
### 4. **复杂曲面加工**
- 四轴加工可以处理复杂的三维曲面,如涡轮叶片、螺旋桨等,适合高难度零件的制造。
### 5. **提高生产效率**
- 四轴加工能够同时进行多轴联动,减少加工步骤,缩短生产周期,提高整体效率。
### 6. **灵活性与适应性**
- 四轴加工适用于多种材料和复杂形状的零件,如金属、塑料、木材等。
- 可根据不同需求调整加工参数,适应多种加工任务。
### 7. **降低人工干预**
- 四轴加工通过程序控制,减少人工操作,降低人为误差,提高加工质量。
### 8. **适用于批量生产**
- 四轴加工适合中小批量生产,能够快速完成复杂零件的加工任务。
### 9. **编程复杂**
- 由于增加了旋转轴,四轴加工的编程比三轴加工更复杂,需要更高的技术水平和经验。
### 10. **设备成本较高**
- 四轴加工中心的价格通常高于三轴设备,初期投资较大,但长期来看可以提高生产效率和产品质量。
### 应用领域
- :加工复杂曲面零件,如发动机叶片、涡等。
- 汽车制造:加工复杂模具、零部件。
- 器械:加工高精度、复杂形状的设备零件。
- 模具制造:加工复杂模具和型腔。
总之,CNC四轴加工通过增加旋转轴,显著提升了加工能力和效率,尤其适用于复杂、高精度的零件制造。
精密零件加工是指通过高精度设备和工艺,制造出尺寸、形状、表面质量等均符合严格要求的零件的加工过程。其特点主要包括以下几个方面:
### 1. **高精度**
- 精密零件加工的核心要求是**高精度**,通常需要达到微米(μm)甚至纳米(nm)级别的公差范围。
- 加工过程中需要严格控制尺寸、形状、位置和表面粗糙度等参数,确保零件符合设计图纸的要求。
### 2. **高表面质量**
- 精密零件对表面质量要求高,通常需要达到镜面光洁度或低的表面粗糙度(Ra值)。
- 表面质量直接影响零件的性能,如耐磨性、耐腐蚀性、密封性等。
### 3. **复杂形状加工**
- 精密零件通常具有复杂的几何形状,如曲面、薄壁、微小孔等,需要借助高精度数控机床(如CNC加工中心)和多轴联动技术来实现。
### 4. **材料多样性**
- 精密零件加工涉及的材料种类广泛,包括金属(如铝合金、不锈钢、钛合金)、非金属(如陶瓷、塑料)以及复合材料等。
- 不同材料的加工特性不同,需要针对性地选择加工工艺和设备。
### 5. **高设备要求**
- 精密零件加工需要高精度设备,如数控机床(CNC)、坐标测量机(CMM)、激光加工机等。
- 设备需要具备高刚性、高稳定性和高重复定位精度,以确保加工质量。
### 6. **严格的过程控制**
- 加工过程中需要对温度、湿度、振动等环境因素进行严格控制,以避免对加工精度产生影响。
- 加工参数(如切削速度、进给量、切削深度等)需要优化,以提高加工效率和表面质量。
### 7. **高成本**
- 精密零件加工的设备、、工艺和技术要求较高,导致加工成本较高。
- 对操作人员的技术水平要求也较高,需要经过培训。
### 8. **广泛应用**
- 精密零件广泛应用于、器械、汽车制造、电子设备、光学仪器等高技术领域。
- 这些领域对零件的性能、可靠性和寿命有高要求。
### 9. **小批量、定制化生产**
- 精密零件加工通常以小批量或单件定制为主,满足特定客户的需求。
- 生产过程中需要灵活调整工艺和参数,以适应不同零件的加工要求。
### 10. **质量检测严格**
- 精密零件加工完成后,需要通过高精度检测设备(如三坐标测量机、光学测量仪等)进行严格的质量检测。
- 检测内容包括尺寸精度、形状精度、位置精度和表面质量等。
### 总结
精密零件加工以高精度、量和高技术要求为核心,广泛应用于制造领域。其加工过程需要高精度设备、严格的过程控制和的技术支持,以确保零件满足设计和应用要求。
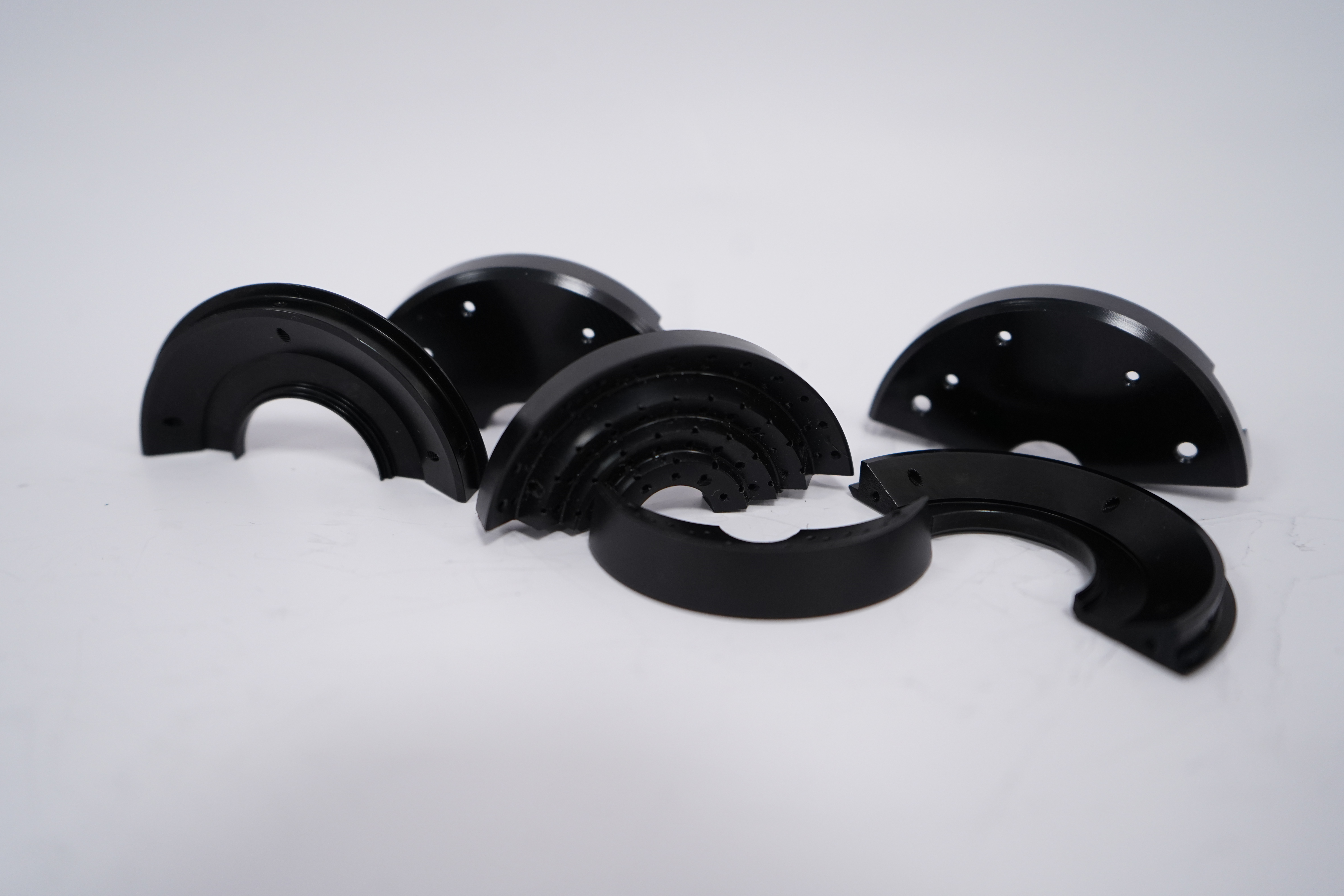
铝合金CNC加工具有以下特点:
### 1. **高精度**
- CNC加工可以实现高的精度,通常可达±mm甚至更高,适合对尺寸要求严格的零件加工。
### 2. **表面质量好**
- 铝合金材料易于切削,CNC加工后表面光滑,无需额外处理即可达到较好的表面光洁度。
### 3. **加工效率高**
- CNC机床可以实现自动化加工,一次装夹完成多道工序,减少人工干预,提高生产效率。
### 4. **材料利用率高**
- CNC加工采用切削方式,可以根据设计需求去除材料,减少浪费,提高材料利用率。
### 5. **适应性强**
- 适用于复杂形状的加工,包括曲面、孔洞、螺纹等,能够满足多样化的设计需求。
### 6. **加工稳定性好**
- CNC机床由程序控制,加工过程稳定,避免了人为误差,保证了零件的一致性。
### 7. **铝合金特性优势**
- 铝合金具有轻质、高强度、耐腐蚀等特性,适合制造、汽车、电子等领域的零部件。
- 铝合金切削性能好,磨损小,延长了寿命。
### 8. **可加工复杂结构**
- CNC加工可以完成传统加工难以实现的复杂结构,如薄壁件、深腔件等。
### 9. **灵活性高**
- 通过修改程序即可调整加工参数,适应不同形状和尺寸的零件加工需求。
### 10. **环保性**
- CNC加工过程中产生的废料少,且铝合金可回收利用,。
总之,铝合金CNC加工以其高精度、率和高灵活性,成为现代制造业中广泛应用的技术。

零部件机加工是指通过机械设备对原材料进行切削、磨削、钻孔、铣削等加工过程,以获得符合设计要求的零部件。其特点主要包括以下几个方面:
### 1. **高精度**
- 机加工能够实现高精度的尺寸控制,通常可以达到微米级别的精度,满足精密零部件的要求。
- 通过数控机床(CNC)等技术,可以进一步提升加工精度和一致性。
### 2. **灵活性**
- 机加工适用于多种材料和形状,可以根据不同的设计需求进行定制化加工。
- 能够处理复杂几何形状的零部件,如曲面、螺纹、孔洞等。
### 3. **材料适应性广**
- 机加工适用于多种材料,包括金属(如钢、铝、铜等)、塑料、复合材料等。
- 不同材料的加工工艺和选择会有所不同,但机加工能够灵活应对。
### 4. **生产效率高**
- 对于批量生产,机加工可以通过自动化设备(如CNC机床)实现、连续的生产。
- 通过优化加工工艺和选择,可以进一步提高生产效率。
### 5. **表面质量好**
- 机加工可以获得较高的表面光洁度,减少后续的表面处理工序。
- 通过精加工和抛光等工艺,可以进一步提升零部件的外观和性能。
### 6. **成本控制**
- 对于小批量或单件生产,机加工具有较低的开模成本,适合定制化需求。
- 对于大批量生产,通过优化工艺和设备,可以降低单位成本。
### 7. **工艺复杂**
- 机加工涉及多种工艺和设备的组合,如车削、铣削、磨削、钻孔等,需要较高的技术水平和经验。
- 工艺参数的设置(如切削速度、进给量、选择等)对加工质量和效率有重要影响。
### 8. **可重复性强**
- 通过数控技术和标准化工艺,机加工能够保证零部件的一致性和可重复性。
- 适合对精度和一致性要求较高的行业,如、汽车制造等。
### 9. **环境污染较少**
- 相比铸造、锻造等工艺,机加工产生的废料较少,且多为可回收的金属屑,环境污染较小。
- 但需要注意切削液和冷却剂的使用和处理,以减少对环境的影响。
### 10. **设备投资大**
- 高精度机加工设备(如CNC机床)的购置和维护成本较高,需要较大的初期投资。
- 设备的更新换代速度较快,需要持续投入以保持技术竞争力。
### 总结
零部件机加工具有高精度、灵活性、材料适应性强等特点,广泛应用于制造业的各个领域。尽管设备投资和工艺复杂性较高,但其、可重复和量的特点使其成为现代制造业的加工方式。
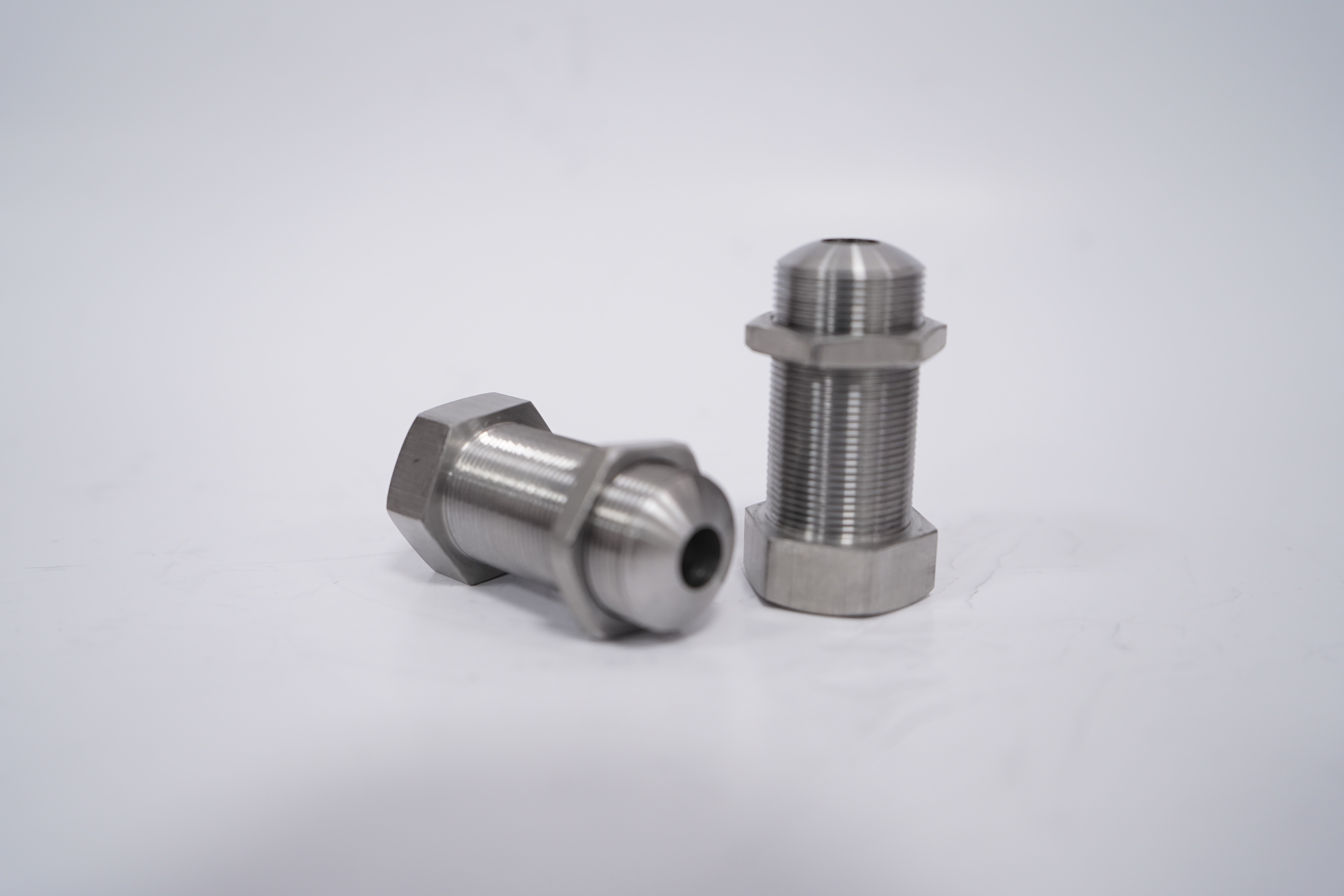
车铣复合加工是一种的制造技术,结合了车削和铣削两种加工方式,具有以下特点:
### 1. **性**
- **一次装夹完成多道工序**:工件只需一次装夹,即可完成车削、铣削、钻孔、攻丝等多种加工工序,减少了装夹次数和时间,提高了加工效率。
- **减少工序转换**:传统加工需要多次装夹和工序转换,而车铣复合加工可以在同一台设备上完成,缩短了生产周期。
### 2. **高精度**
- **减少装夹误差**:由于工件只需一次装夹,避免了多次装夹带来的定位误差,提高了加工精度和一致性。
- **动态补偿功能**:现代车铣复合机床通常配备高精度数控系统和动态补偿功能,能够实时调整加工参数,确保加工精度。
### 3. **灵活性**
- **复杂零件加工**:车铣复合加工可以处理复杂形状的零件,如带有曲面、斜孔、异形槽等特征的工件,传统单一加工方式难以完成。
- **多轴联动**:车铣复合机床通常配备多轴(如4轴、5轴甚至更多),能够实现多轴联动加工,扩展了加工范围和灵活性。
### 4. **节约成本**
- **减少设备投资**:传统加工需要多台设备(如车床、铣床等),而车铣复合加工只需要一台设备,降低了设备采购和维护成本。
- **减少人工成本**:由于自动化程度高,减少了人工干预和操作,降低了人工成本。
### 5. **材料利用率高**
- **近净成形加工**:车铣复合加工可以实现近净成形加工,减少材料浪费,提高材料利用率。
- **减少毛坯余量**:由于加工精度高,毛坯余量可以设计得更小,进一步节约材料。
### 6. **适应性强**
- **多种材料加工**:车铣复合加工适用于多种材料,包括金属、塑料、复合材料等,适用范围广。
- **小批量、多品种生产**:特别适合小批量、多品种的生产模式,能够快速切换加工任务,适应市场需求变化。
### 7. **智能化**
- **数控系统支持**:现代车铣复合机床通常配备的数控系统,支持自动编程、仿真和优化,提高了加工过程的智能化水平。
- **自动化集成**:可以与其他自动化设备(如机器人、自动送料系统等)集成,实现无人化或半无人化生产。
### 8. **环保性**
- **减少能耗**:由于减少了设备数量和加工时间,车铣复合加工在能耗方面更加环保。
- **减少废料**:高精度加工减少了废料产生,降低了环境污染。
### 总结
车铣复合加工以其、高精度、灵活性强、节约成本等特点,在现代制造业中得到了广泛应用,特别适合复杂零件加工和高精度要求的生产场景。随着数控技术和自动化技术的不断发展,车铣复合加工的应用前景将更加广阔。
电子配件外壳加工具有以下几个显著特点:
### 1. **高精度要求**
- 电子配件外壳通常需要与内部电路板、接口、按键等精密配合,因此对尺寸精度、形状公差和表面光洁度要求高。
- 加工过程中需要使用高精度设备(如CNC加工中心)以确保尺寸和形状的准确性。
### 2. **材料多样性**
- 外壳材料种类多样,常用的包括铝合金、不锈钢、塑料(如ABS、PC)、合金等,不同材料需要采用不同的加工工艺。
- 材料的选择需考虑强度、重量、散热性、电磁屏蔽性以及成本等因素。
### 3. **复杂结构设计**
- 电子外壳通常具有复杂的结构,如开孔、螺纹、卡扣、散热孔等,以满足功能性需求。
- 加工时需要兼顾外观美观性和功能性,同时确保装配的便捷性。
### 4. **表面处理工艺**
- 外壳通常需要经过表面处理以提升外观和耐用性,常见的工艺包括阳氧化、喷砂、电镀、喷涂、拉丝等。
- 表面处理还需考虑防腐蚀、耐磨性、抗指纹等性能。
### 5. **散热设计**
- 电子设备运行时会产生热量,外壳设计需考虑散热性能,如增加散热孔、散热片或使用导热材料。
### 6. **电磁屏蔽**
- 外壳需要具备一定的电磁屏蔽能力,以减少外部电磁干扰对内部电路的影响,通常通过金属材料或特殊涂层实现。
### 7. **小批量、定制化生产**
- 电子配件外壳通常根据特定产品需求进行定制化设计和生产,因此加工具有小批量、多品种的特点。
- 快速响应市场需求和灵活调整生产工艺是重要竞争力。
### 8. **环保与安全性**
- 外壳材料需符合环保标准(如RoHS、REACH),避免使用有害物质。
- 设计需考虑防水、防尘、防震等安全性要求。
### 9. **成本控制**
- 在和功能的前提下,需要优化加工工艺和材料选择以降,满足市场竞争需求。
### 10. **快速迭代**
- 电子产品更新换代快,外壳加工需要适应快速设计和生产的节奏,缩短从设计到量产的周期。
总之,电子配件外壳加工是一项集高精度、多功能性、定制化和快速响应于一体的综合性制造工艺,需要综合考虑设计、材料、工艺和成本等多方面因素。
http://www.szruitongjm.com